sheet metal piercing process What is Piercing? Piercing is a metal fabrication technique that creates holes in sheet metal. It uses a punch to penetrate the material, forming an opening without removing any metal. The process displaces the material, often creating a . Legrand Wiremold NMW35 Nonmetallic Plastic Raceway for Extending Power, 1 Gang Extra Deep Outlet Box, 1 3/4" Deep, White (1 Pack) Visit the Wiremold Store 4.5 4.5 out of 5 stars 77 ratings
0 · punching operation in sheet metal
1 · nibbling operation in sheet metal
2 · embossing operation in sheet metal
3 · difference between piercing and punching
4 · difference between piercing and blanking
5 · cutting operation in sheet metal
6 · blanking operation in sheet metal
7 · blanking and piercing diagram
Learn how to calculate box fill accurately for efficient and safe wiring. Enhance your electrical knowledge with this formal guide.Explore the latest connectivity and structured wiring products from On-Q. Designed for professional installers, On-Q brings homes to life. NEW! Enclosure Inside Accessories. The .
Punching blanking and piercing are sheet metal shearing operations to modify existing blank. Similar machines but different punch and .
Piercing is a metal fabrication process that create precise holes in sheet metal. The punch penetrates the material to create an opening, but it doesn’t remove any metal. It typically displaces the material while creating a .There are various types of blanking and piercing: lancing, perforating, notching, nibbling, shaving, cutoff, and dinking. Lancing is a piercing operation in which the workpiece is sheared and bent with one strike of the die. A key part of this process is that there is not reduction of material, only a modification in its geometry. This operation is used to make ta.What is Piercing? Piercing is a metal fabrication technique that creates holes in sheet metal. It uses a punch to penetrate the material, forming an opening without removing any metal. The process displaces the material, often creating a .
Explaining the Basic Difference Between Blanking, Piercing and Punching Process with the Help of this AnimationSheet Metal Forming/Shearing Process:Blanking-. For one-off parts and small production runs, other cutting processes, such as laser cutting, tend to be more cost-effective. Explore the three primary shearing processes (shearing, blanking, punching) utilised by the . There are five types of processes that are generally used in press-work sheet-metal forming: (a) open shearing, (b) blanking, (c) piercing, (d) bending, and (e) deep drawing. .It focuses on blanking and piercing operations in a press tool to form and shape the final part geometry. The types of piercing operations include conventional piercing, piercing with a pointed punch, piece-and-extrude operations, slotting, .
Many shearing, blanking, and piercing operations are based on the same underlying principles of shear mechanisms. This article provides information on the various operations associated with . Explaining the Basic Difference Between Blanking, Piercing and Punching Process with the Help of this AnimationSheet Metal Forming/Shearing Process:Blanking-. Piercing is a shearing process in which raw metal is pierced with a machining tool, resulting in the creation of a circular or other shaped hole. . The key thing to remember is that blanking results in the creation of multiple metal .
The fundamental goal of sheet metal forming procedures is to give the metal sheets particular geometrical modifications while preserving their structural integrity. The common types of sheet metal operations are shearing, . The sheet metal blanking process is a fundamental aspect of the manufacturing industry that converts flat metal sheets into specific, predefined shapes for a variety of uses. This method is known for its efficiency and is especially advantageous for high-volume production. Let’s take a closer look at how sheet metal blanking operates. In this paper section, a description of the innovative dieless cryogenic tube piercing process is provided. A conceptual comparison between the regular tube punching process and the cryogenic dieless punching is reported in Fig. 1 a) and c). Since some materials show a ductile-to-brittle transition at cryogenic temperatures, the possibility to pierce a tube .To refine the surface of your metal, you'll use sandpaper across a gradient of grits from (relatively) coarse to fine. Most hardware stores carry sheets of wet-dry sandpaper; pick up a sheet each of 400, 600, and 800 grit.You can tape sandpaper to a flat surface to create a mini sanding board, and get sanding boards that work like nail files.If you don't plan to polish your projects with a .
Hello Friends Today we will discuss about the Punching and Blanking in this topic with detail example.#Punching, #Piercing, #Blacking, #Punching&Blancking, T.
Metal piercing is the process of cutting designs, shapes and holes into metal components that are used to create jewelry pieces. It is an essential skill. . punches for sheet metal, sheet metal cutters, sandpaper or abrasive strips, a hammer, a bench pin and an anvil or vice. You should also consider purchasing earring converters if needed . In the realm of sheet metal fabrication, where precision and efficiency reign supreme, self-piercing riveting (SPR) emerges as a transformative technology, revolutionizing the way we assemble sheet metal components. Introduction SPR defies conventional joining methods by eliminating the need for pre-punched holes. Instead, a specially designed SPR tool pierces . Subject - Manufacturing Processes, MetallurgyChapter - Difference between Blanking, Piercing, Punching, Lancing, Notching Process, Sheet metal WorkingTimecod.
punching operation in sheet metal
3.1 Shearing: Principle of Operation. Shearing, or open shearing, is a sheet-metal cut-off operation along a straight line between two cutting edges.In shearing, a piece of sheet metal is separated by applying a shearing force that is high enough to exceed the ultimate shear strength of the material; the excessive applied shear stress causes fracture and separation at .Process Home: Sheet Metal: Bending: CNC Fabrication: Laser Cutting: Shearing: Staking: Stamping Blanking Deburring Drawing Forming Gage of Sheet Metals Machining: Piercing: Welding: Resources: Bibliography: . Piercing is the operation of cutting internal features (holes or slots) in stock. Piercing can also be combined with other operations .
Chapter 1 Roll Forming in Sheet Metal Forming: Principles and Processes . Suman Deb. Chapter 2 A Systematic Review of the Rotary Piercing Process . Pravin Pawar, Amaresh Kumar, and Raj Ballav. Chapter 3 Finite Element Analysis of the Metal Spinning Process . N. Balaji and D. Nagarajan. Chapter 4 High-Energy Rate Forming . Jagadeesha T. Chapter 5 The Formability .
Blanking and piercing are manufacturing processes by which certain geometrical shapes are sheared off a sheet metal. If the sheared off part is the one required, the processes referred to as . SHEET METAL PROCESS - Download as a PDF or view online for free. Submit Search. . Punching or Piercing: Punching operation is producing the hole on the workpiece by a punch. In punching, the removed metal is called . The only difference between perforating and piercing is the coverings in every hole. 8. Slotting. Slotting is a sheet metal process where a slot is put in the metal to do its job. Also known as slitting, the machines used in .
Analysis and Optimization of Sheet Metal Forming Processes comprehensively covers sheet metal forming, from choosing materials, tools and the forming method to optimising the entire process through finite element .A sheet metal stamping process is a metalworking process carried out at room temperature wherein parts are both cut and shaped from a parent metal strip or. . the next step would be a piercing process. If the part is a shallow dish with a hole in the bottom, the next two steps would be forming and piercing. . Even after the development of various non-conventional processes for sheet metal cutting, the shearing process remains the most preferred process in mass production.
Piercing is a shearing operation in which raw metal is pierced with a machining tool to form different shapes. Rotary piercing is the process that is mostly used for making seamless tubes after producing the desired alloy ingot. In this process, the material is subjected to shearing deformation due to rotary forging. So having a basic idea about sheet metal fabrication process is important before we jump into Blanking, Piercing, and punching. Sheet metal fabrication is a metalworking process to cut and form .Piercing: It is a distinct process of making a hole in sheet metals. It is characterized by: (a) The punch is sharp and pointed tool which is able to penetrate or pierce through the sheet metal. (b) There is no scrap from the hole. (c) The hole has rough flanges around the hole. Notching: 1. Introduction. Laser beam cutting of sheet metal usually starts with a piercing process. The maximum sheet thickness s that can be pierced and cut has increased with the increase of the available laser power. The application of suitable piercing parameters is mandatory to obtain a successful and fast piercing process.
Metal stamping is a complex process that can include a number of metal forming processes — blanking, punching, bending, and piercing, to name a few. . Piercing Piercing is a common metal stamping process and ideal for forming holes and slots fully enclosed . Burr allowance is generally 10% of the thickness of the sheet material. To .
nibbling operation in sheet metal
how to fix loose electrical box in wall
Sheet metal punching is the process of creating holes in sheet metal using a punch press or a CNC punching machine. The process involves cutting and piercing the sheet metal using dies mounted on presses. Different metals require specific pressure for punching, and the process involves creating holes of various shapes and sizes. .
As the minimum size is important in piercing/punching, the punch is made equal to the hole size. The Die clearance on the die cut out is bigger than the size stated on the component drawing. . A stamping press machine is a machine that can process sheet metal into the desired shape. It is commonly used for metal stamping to convert a flat .Sheet Metal Embossing Process Animation in SolidworksEmbossing:It is a Metal Forming Process for Producing raised or sunken designs in sheet metal material b.

how to get to the last junction box starfield
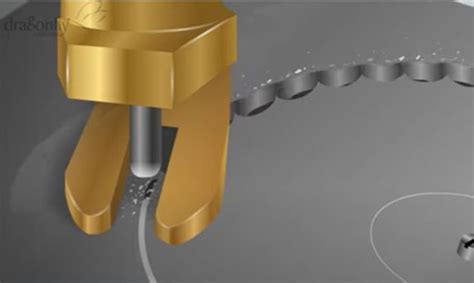
embossing operation in sheet metal
If wires are not twisted tight in a junction box, you touch the wire nut and it falls to the floor while the wires separate. Prior to touching the wire nut, could this poor connection cause a sparking and a fire?
sheet metal piercing process|cutting operation in sheet metal